The first effective action in controlling the contamination of hydraulic fluids and lubrication, is to prevent it from entering the system
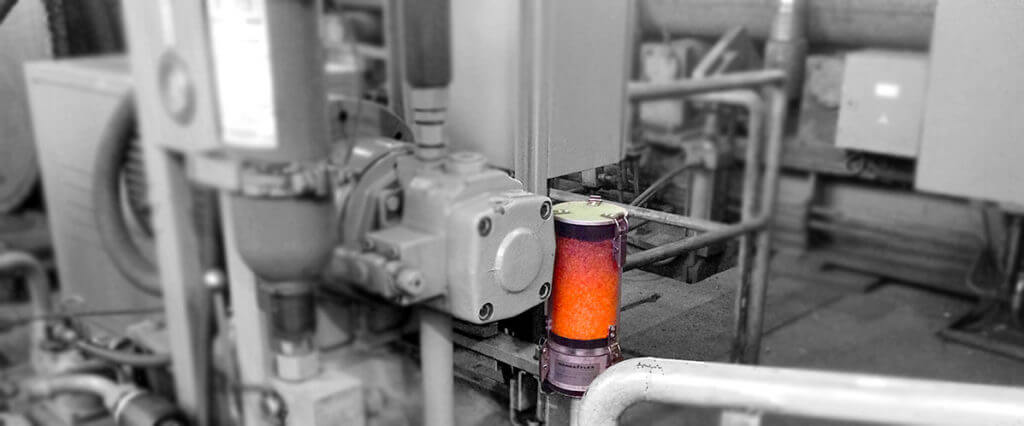
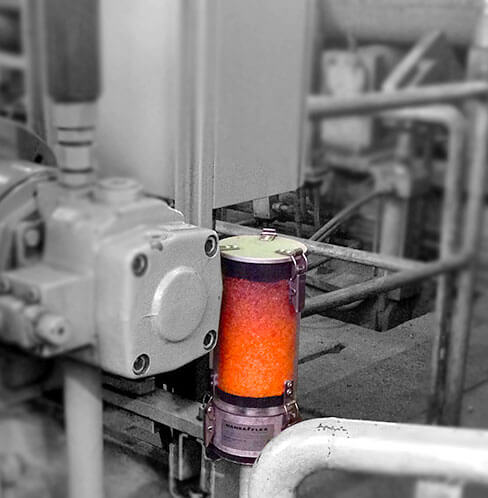
In order to manage an effective lubrication programme, one needs to consider all the factors that influence the performance of the system and the lubricant’s service life. Using the proper air vent to rule out external contamination is one of the most important factors.
Systems such as gearboxes, pumps, tanks, oil drums, must breathe when the air in the ventilation space undergoes expansion and contraction due to temperature changes or to changes in the oil level in oil-hydraulic circuits, the return fluid and the actuator range cause changes in the volume of air between the top oil level and the tank’s cover. Each time the system “breathes”, solid contamination and moisture enter the circuit and contaminate the lubricant, causing damage to the components installed on the machine over time.
Since it is apparent that at least half the contamination in a circuit is transferred from the external environment and that most systems are designed to “breathe”, it is essential to stoop solid and liquid contamination at the origin. How? By installing efficient air venting filters capable of removing both solid and liquid contamination.
Absorbent and particle venting filters use the natural properties of two of the most effective absorbent substances in nature, silica gel and activated carbon.
Silica gel absorbs and holds water by about 40% of its weight, when moisture goes through the filter it is trapped in the pores of silica gel, drying the air entering the tank and removing any residual moisture. An inorganic fibre or membrane filter installed within the filter, holds and removes solid particles sized ≤ 3 um from the inlet air. The air thus purified enters the tank without any external contamination.
products menu
▽